what you’ve wanted for an innovative tooling solution.


• Minimized chattering of workpiece due to minimum lead angle and sharp cutting edge
• Reduced cutting resistance and improved chip emissions by high helix angle application
RM14
In the various industries including automotive components business, workpieces are manufactured with casting for easy-producing complicated shapes and lowering cost. However, due to the characteristic of casting manufacturing, facing is necessary on each uneven facing surface for assembling.
In casting machining, complicated shapes of workpiece and uneven surface creates low clamping force, chattering, unstable tool life, bad surface finish and even shortening life of equipment.
KORLOY launches the double-sided face mill, RM14 to solve those troubles in machining.
RM14 designed with the maximum lead angle, 51˚ of heptagonal shape reduces cutting load and chattering comparing to the conventional face mill with lead angle, 45˚. Its strong wedge type clamping system ensures stable tool life even in poor cutting conditions.
In addition, there are two types of RM14 insert which are neutral (flat cutting edge) and right-handed (helix cutting edge) and it is possible for both of them to clamp to a single holder. The thicker RM14 insert with sharp cutting edge ensures good performance and stability and its optimal grade realizes long tool life.
RM14 is an economic tool using maximum 14 corners and ensures stable machining and high productivity.
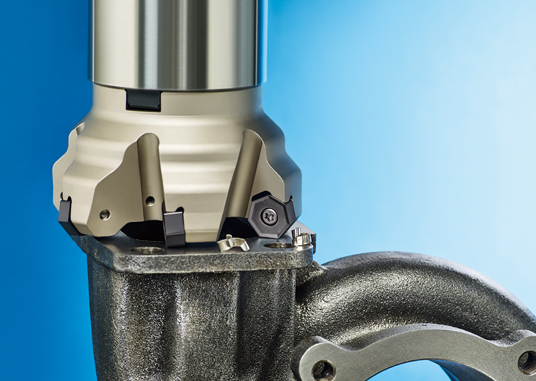
• Good performance
- Less cutting load due to high rake and high helix
• Stable tool life
- High rigidity from thick insert
• Improved surface finish
- Less chattering due to lead angle of 51˚
- Good chip evacuation
• Stable clamping system
- Wide supporting area and acute angled clamping structure