what you’ve wanted for an innovative tooling solution.


• The optimal substrate for cast iron cutting with coating adherence technology ensures regular tool life
PC6100
In cast iron machining, the formation of short, broken chips results in a lower load on the rake face of the insert, leading to slower wear progression. However, the relief surface, which comes into direct contact with the workpiece, experiences longer friction time and therefore wears out relatively quickly.
Especially, nodular graphite cast iron, compared to gray cast iron, has high hardness and high toughness characteristics. During machining, it forms built-up edges and adhesion on the surface of the insert, causing uneven chipping. Additionally, to remove the dust generated during machining, wet machining is mainly used. The cutting fluid rapidly cools the heated insert, repeatedly subjecting the cutting edge surface to significant thermal shock, which causes thermal cracks and coating delamination on the cutting edge.
KORLOY launched PC6100, a grade for cast iron milling that can enhance productivity.
PC6100 applies a new coating technology called "Ion Plus - Tech™," which suppresses layer delamination and thermal crack formation, providing excellent tool life and reliability. Additionally, by using a substrate optimized for cast iron machining, it offers superior wear resistance and impact resistance.
Through this, PC6100 demonstrates excellent performance in cast iron machining under various conditions, and particularly in ductile cast iron machining, you will experience superior tool life and machining reliability
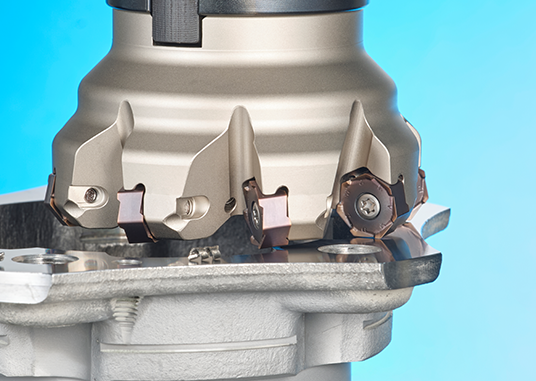
• Good wear resistance and adherence of layer
- Individual PVD coating technology Ion Plus-Tech™
• Stable tool life
- Optimal wear resistance and fracture resistance substrate for cast iron cutting
• Reduced chipping and unexpected fracture
- Coating surface treatment